Toy
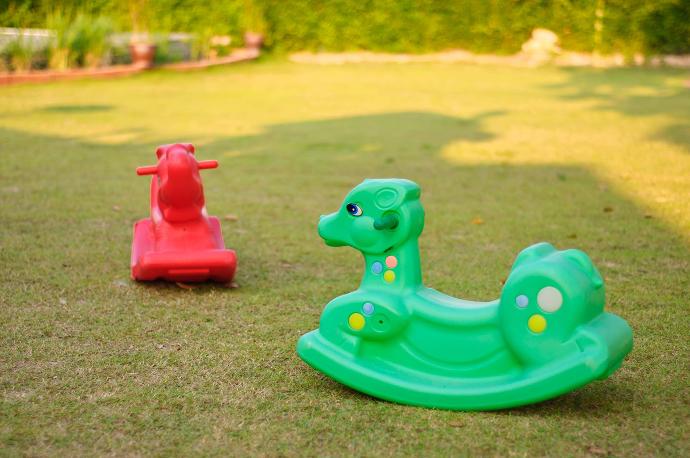
Blow molding is a crucial manufacturing process in the toy industry, providing toy manufacturers with the capabilities to produce safe, durable, and appealing toys at scale. Blow molding toys offer various applications and benefits, let's introduce you below.
What’s the advantage of using Blow Molding Toy?
Blow molding offers numerous advantages in the toy manufacturing industry, including accessibility, efficiency, flexibility, and quality assurance. Its ability to produce a wide range of toys quickly and cost-effectively makes it an invaluable manufacturing technique for toy producers worldwide.
- Design Flexibility: Blow molding offers great freedom in design, allowing manufacturers to create toys of various shapes, sizes, and complexities. The use of molds enables precise control over the final product, ensuring consistent quality and accuracy in toy production. Additionally, the ability to mix colorants directly into the plastic material allows for vibrant and colorful toy designs, enhancing their appeal to consumers.
- Easy Malleability: Blow molding allows for the use of a wide range of plastic resins, offering flexibility in material selection. This enables manufacturers to choose the most suitable polymer for each toy, ensuring the desired level of hardness, malleability, and durability.
- Safe and Durable Materials: Blow-molded toys are made from safe and durable plastic materials, ensuring that they can withstand rough play and handling by children. These materials are also lightweight, making the toys easy to carry and manipulate, while still being robust enough to endure everyday use.
- Mass Production: Blow molding enables large-scale production of toys at an accessible cost. With the use of molds, manufacturers can produce toys in high volumes, meeting the demand of the market efficiently. This scalability allows for cost-effective production and ensures that popular toys can be readily available to consumers.
- Customization and Personalization: Yu Ching blow molding service enables the customization and personalization of toys, allowing manufacturers to create toys with unique designs, colors, and features. This customization enhances the appeal of toys to children and allows manufacturers to cater to specific market preferences and trends.
Applications of Plastic Blow Molding in Toy Devices
Blow molding finds use in producing certain types of toys, especially those that require hollow or hollow-like structures. Here are some common applications of blow molding in the toy industry:
- Hollow Toys: Blow molding is commonly used to produce hollow toys such as balls, balloons, and various inflatable toys. The process allows for the creation of lightweight and durable toys with a hollow interior, making them suitable for activities like bouncing, throwing, and floating.
- Outdoor Play Equipment: Blow molding is also used to manufacture outdoor play equipment such as slides, swings, and playhouses. These larger toys often require hollow components for structural support and are typically made from durable plastics to withstand outdoor conditions.
- Water Toys: Blow molding is ideal for producing water toys such as water guns, squirt toys, and pool floats. The hollow structures created through blow molding make these toys lightweight and buoyant, allowing them to float on water and provide hours of fun for children during water play activities.
- Novelty Items: Blow molding is used to create various novelty items and party favors, including piggy banks, bubble blowers, noise makers, and novelty containers. These toys often feature unique shapes and designs that are easily achievable through blow molding.
Blow molding offers several advantages in the toy manufacturing industry, making it a preferred method for producing various types of toys. Here's why blow molding is commonly used in the creation of toys. Yu Ching's outstanding production capabilities have allowed our products to encompass many children's lives. If you want to inquire about other blow molding toys or custom plastic toys, feel free to send us an e-mail.