Blow Molding
OEM & ODM
Starting from your requirements, Yu Ching's R&D team will conduct research and collaborate with yours to design and propose effective suggestions and solutions, significantly reducing the development timeline.
We offer a one-stop service that includes customized mold design, manufacturing, and final packaging and shipping. This eliminates the need for clients to select different companies for manufacturing different product lines, saving communication time and creating the highest level of competitiveness for our clients.
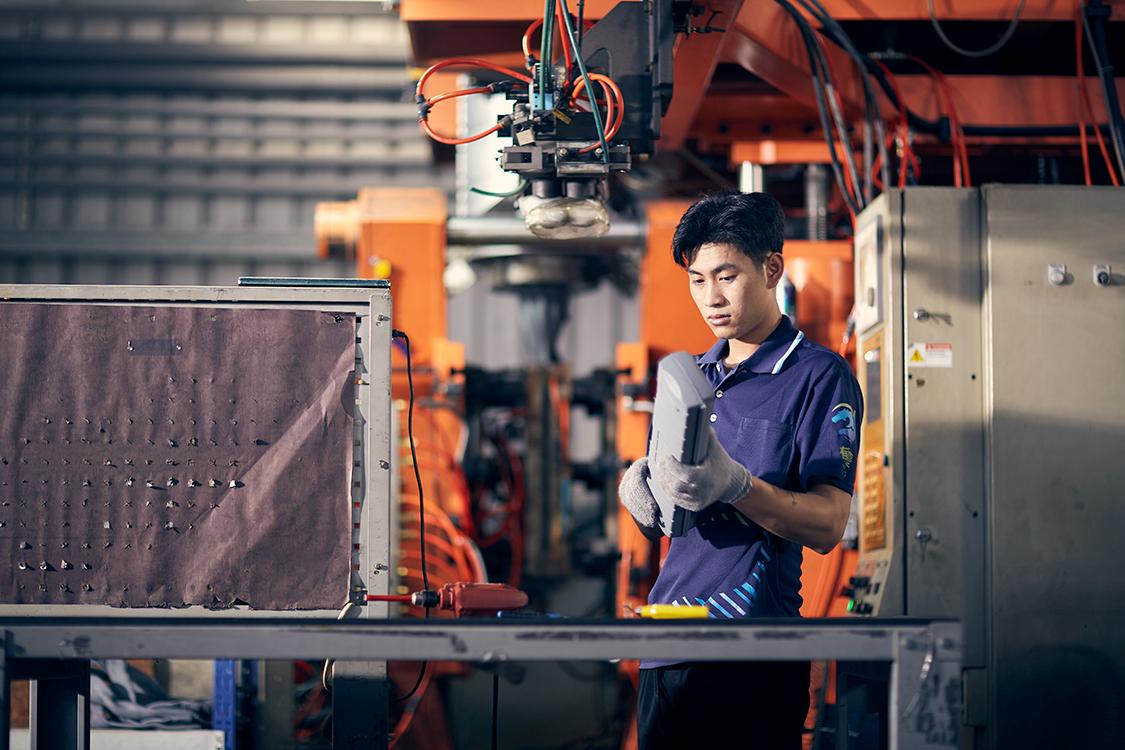
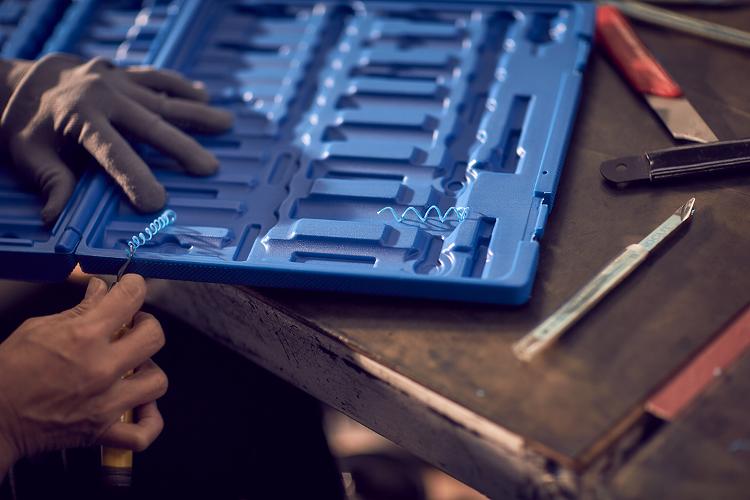
Yu Ching possesses professional and technical knowledge in blow molding and design manufacturing, enable to provide excellent products to our clients. We specialize in producing various shapes and complex blow-molding products, and our skilled team utilizes advanced technique to ensure that each product meets the highest quality standards and complies with client specifications. Our services are customizable to meet the needs of each client, and we work closely with our clients throughout the process, aiding from design to processing to ensure complete satisfaction.
We understand that both designing and manufacturing products are equally important, which is why our experienced design engineers utilize the latest software to help you create economical, efficient, precise, and functional blow molding designs.
Yu Ching is dedicated to delivering excellent blow molding services and becoming a trusted partner for clients across industries. Please contact us to learn more about our blow molding capabilities and how we can assist you in achieving your goals.
Differences between Blow Molding and Injection Molding
Molding Process
Blow Molding
It is a process where high-pressure air is used to blow plastic raw material into hollow products.
Injection Molding
It involves injecting plastic raw material into a mold, allowing it to cool and solidify to form the product.
Material Selection
Due to the differences in the molding processes, the characteristics and performance requirements of the plastic materials used are also different.
Blow Molding
Requires thermoplastic materials with certain expandability and plasticity.
Injection Molding
Requires plastic materials with good flowability and melt stability.
Application Areas
Blow Molding
It is primarily used for manufacturing hollow products such as plastic bottles, containers, and toys. Since these products require internal space, blow molding is the most suitable method.
Injection Molding
It is suitable for various shapes and sizes of plastic products, including parts, casings, accessories, toys, and household appliances. Injection molding offers greater flexibility and can produce a wider range of products.
Blow Molding Production Process
01. Material Inputting
Depending on the machine type, plastic is inputted and heated through a screw.
02. Plasticization and Extrusion
The plastic is heated to a temperature within the plasticity range. The machine extrudes the plastic into a parison and closes the mold, covering the parison.
03. Blow Molding
High-pressure air is injected into the parison, causing it to inflate and cling to the mold's interior, forming its shape.
04. Mold Release after Cooling
After the plastic has cooled, the mold can be opened, and the finished product can be removed.
One-Stop Service Flowchart
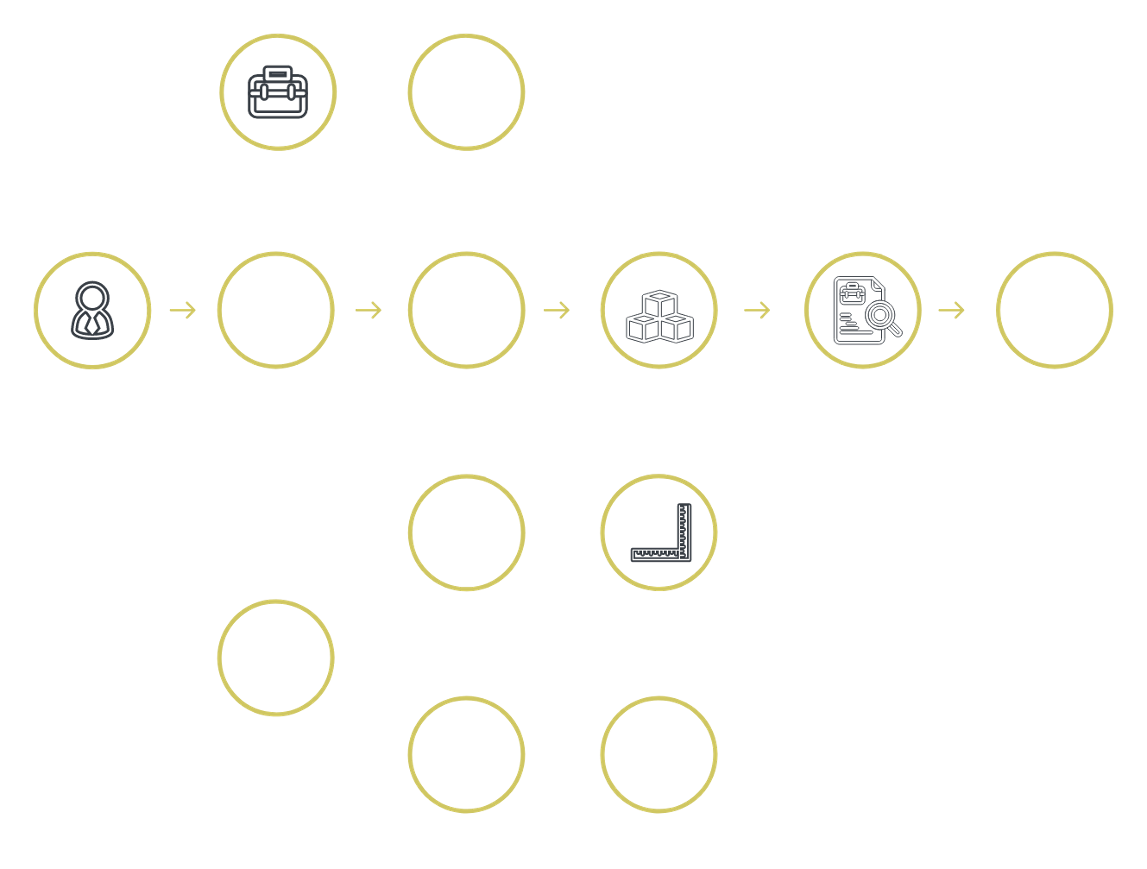
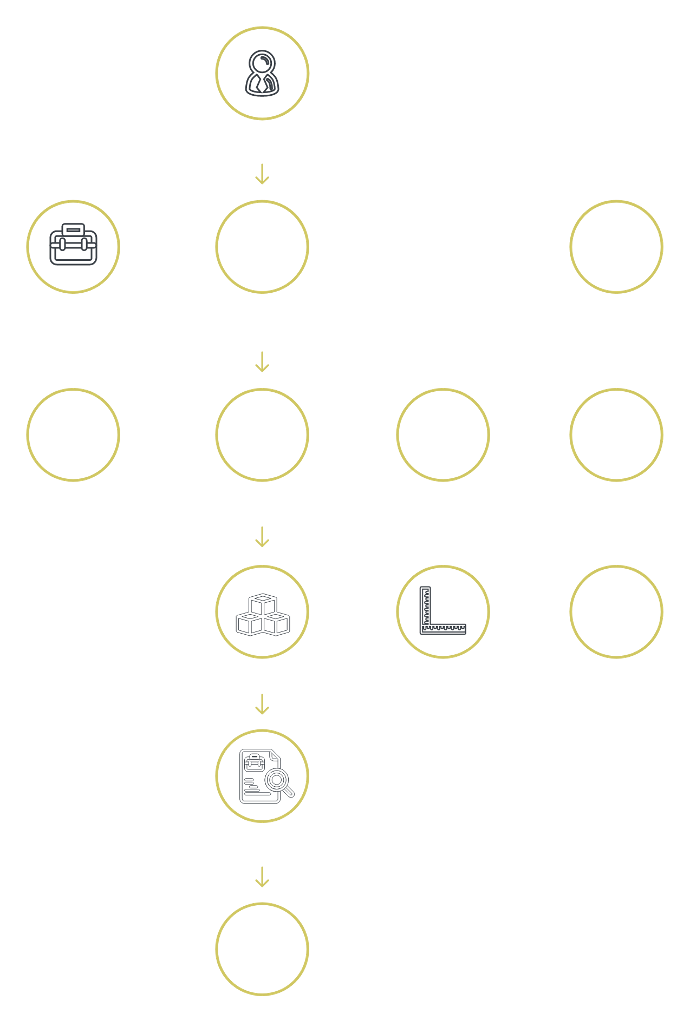